Blog
Oak Hall Produces Face Masks for Healthcare Workers during COVID-19
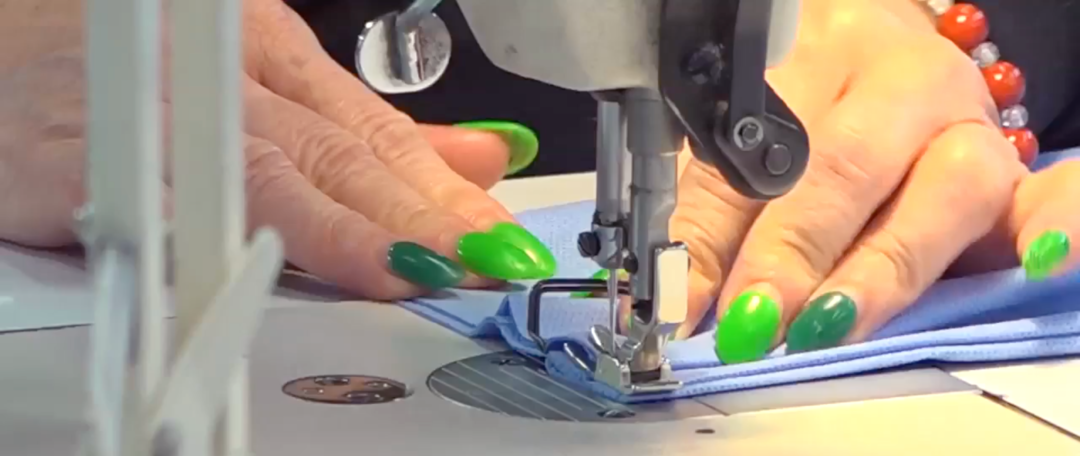
In this time of global crisis due to the COVID-19 pandemic, we’re all doing our best to make it day by day. It’s been hard watching students deal with the disappointment of their college commencement ceremonies being canceled across the nation and the world. Commencement ceremonies are the reason we’ve existed since 1889, and it’s a season we look forward to every day of the year.
But that doesn’t mean that we aren’t staying busy. Instead of our employees sewing our classic regalia and mortarboard hats, we’ve decided to do our small part to help our community on the East Coast and even across the country.
In partnership with Johns Hopkins University, we’re putting our 300 sewing employees to work sewing N95 face masks to alleviate the personal protective equipment (PPE) shortage being experienced across the country.
“Johns Hopkins has provided the fabric for us so it was fully tested, fully approved by them,” said Joe D’Angelo, Oak Hall’s president.
Time is of the essence as we confront the coronavirus, so Johns Hopkins brought the fabric to our warehouse in Salem, Virginia, as quickly as possible so we could get started. “The shipment arrived here Monday night with their couriers, so we could start production on Tuesday,” said D’Angelo.
Even though our company has never made face masks before, it didn’t take long for our expert staff to get to work creating something that will save people’s lives.
“It’s humbling to be able to play a part in alleviating this crisis,” said Donna Hodges, Executive Vice President. “After all of these years being here, I never would have thought we’d be faced with this, but we’re glad that our company is well-equipped to meet this need.”
“Our commitment to Johns Hopkins will be to produce 1.3 million masks,” said D’Angelo. Though many more masks will be needed to confront COVID-19, we’re happy that this will go a long way to helping nurses and doctors on the front lines.
In the meantime, we’re taking the necessary precautions to keep our employees safe. Each sewing station is placed more than 6 feet apart, and only employees are allowed inside.
“We’ve never laid off workers, ever, in our 130 years of being in business,” said Hodges, “and we don’t plan on starting any time soon. It feels good to put our employees to work, even if it’s not on our caps and gowns that we love so much, and even better that it’s meeting a serious medical need in our country right now.”